
Fabrication Capabilities
At ExMesh Engineering, we specialise in high quality fabrication services tailored to meet the diverse needs of industries worldwide. Our advanced capabilities include precision laser cutting, CNC press braking, and bespoke welding solutions, ensuring every project is completed with exceptional accuracy and efficiency. Whether you’re looking for custom metal components, structural frameworks, or intricate designs, our skilled team delivers innovative solutions that exceed expectations.
fabrication Capabilities
See some fabrication in action.
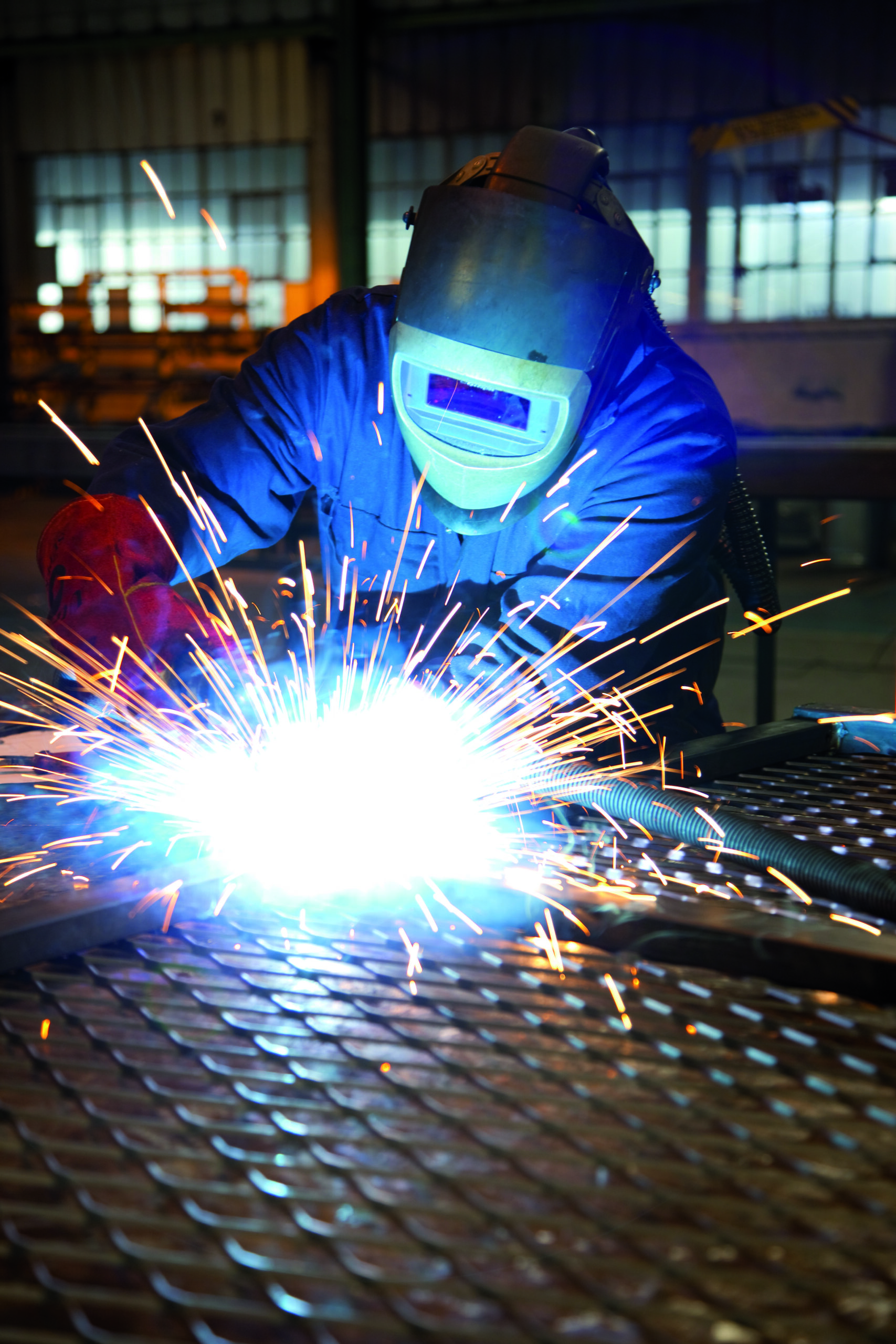
With our comprehensive manufacturing facilities and advanced engineering proficiency, we proudly present a diverse array of specialised fabrication capabilities in the realm of metalwork. Notably, our expertise extends beyond the production and provision of expanded metal mesh products. We possess the requisite skills and experience to cater to multifarious fabrication requirements.
This strategic positioning affords our clientele the distinct advantage of a consolidated solution, whereby the procurement of our expanded metal mesh products seamlessly integrates with ancillary fabrication needs. By obviating the necessity for engaging external providers, we streamline operations, enhance efficiency, and furnish substantial cost and time savings for our esteemed patrons.
Moreover, our adeptness extends beyond conventional boundaries, enabling us to craft bespoke metal products tailored to unique specifications. This bespoke service underscores our commitment to innovation and customer-centricity, thereby fortifying our position as a trusted partner in metal fabrication.
MIG WELDING (STEEL/ALUMINIUM)
MIG welding, or Metal Inert Gas welding, is a widely used and versatile welding process. It involves the use of a consumable wire electrode that melts and fuses with the workpieces, creating a strong and durable weld. The process is characterised by the use of a shielding gas, which protects the weld pool from atmospheric contaminants, ensuring clean and high-quality welds and it is known for its efficiency, speed, and applicability to various materials, making it suitable for a range of industries. The process is employed in diverse applications, from automotive and construction to fabrication and manufacturing.
The functionality of a cobot, or collaborative robot, complements MIG welding processes by offering automation capabilities. Cobots can assist in tasks such as material handling, part positioning, and operating the welding equipment itself, enhancing efficiency, precision, and safety in the welding process. Their ability to work alongside human operators in a collaborative manner makes them valuable assets in modern manufacturing environments, where productivity and flexibility are paramount.
CNC PRESS BRAKING
Press braking is a metal forming process that involves bending/folding and shaping sheet or plate materials using a press brake machine. In this technique, a punch exerts force on the workpiece against a die, causing it to deform and take on the desired shape. Press braking is widely utilised in industries such as metal fabrication, construction, and manufacturing for creating components with precise angles and bends.
The process offers versatility in producing a variety of geometries, making it suitable for complex and intricate designs. Press brakes come in various sizes and configurations, allowing for flexibility in handling different materials, thicknesses, and sizes. Known for its accuracy and efficiency, press braking is a fundamental method for shaping sheet metal into components used in a diverse range of applications.
DESIGN SUPPORT, 2D AND 3D CAD
Our 2D and 3D CAD design support services offer detailed digital modelling of your products or components. With 2D CAD, we create precise flat drawings perfect for layouts and schematics, while 3D CAD allows us to build fully interactive models that you can view from any angle.
This service ensures your designs are thoroughly planned, visualised, and refined before production, improving accuracy and efficiency. It’s an invaluable tool for ensuring your project meets all specifications, making the entire process smoother and more reliable.
LASER PROFILING
Laser profiling is a precision cutting technique that uses a focused laser beam to cut or engrave metal materials with high accuracy. The process offers clean, precise edges, making it ideal for creating complex shapes and intricate designs.
Laser profiling is widely used in industries such as manufacturing, automotive, and aerospace, where precision and consistency are critical. This method is especially valued for its speed and ability to handle various thicknesses of metal without physical contact, reducing the risk of material deformation.
PLASMA CUTTING
Plasma cutting is a highly efficient metal cutting process that employs a focused jet of ionised gas, or plasma, to melt and remove material. This technique is widely utilised in metal fabrication, construction, and industrial applications due to its precision and versatility. A plasma cutter generates an electrically conductive plasma arc, reaching temperatures capable of swiftly cutting through various metals, including steel, aluminium, and stainless steel.
The process offers exceptional speed and accuracy, making it suitable for intricate shapes and designs. Plasma cutting machines can be computer numerically controlled (CNC), allowing for automated and programmable cutting, enhancing efficiency and repeatability. This method is valued for its ability to handle a range of material thicknesses, making it a preferred choice for industries requiring fast and precise metal cutting for diverse applications.
WIRE EROSION
Wire electrical discharge machining (Wire EDM) is a precision machining process that employs electrical discharges to shape and cut conductive materials. In this method, a thin, electrically charged wire, typically made of brass or tungsten, serves as an electrode. The wire is carefully guided through the workpiece, creating controlled electrical discharges that erode the material.
This technique is renowned for its exceptional accuracy in producing intricate and complex shapes in materials such as metals and alloys. Wire EDM is particularly valued in industries requiring high-precision components, such as aerospace, medical, and toolmaking. The process allows for tight tolerances and fine finishes, and its non-contact nature minimises mechanical stresses on the workpiece.
Additionally, Wire EDM can efficiently handle hard materials, making it a versatile and indispensable technology for achieving precise and intricate geometries in various manufacturing applications.
CNC CUTTING
CNC cutting is a precise manufacturing process where a computer-controlled machine uses various tools to cut materials according to digital designs. The process allows for high accuracy and consistency, making it ideal for complex shapes and detailed work. CNC (Computer Numerical Control) machines operate autonomously, following programmed instructions increasing production efficiency.
Common CNC cutting techniques include milling, turning, and laser cutting, all of which are essential in industries such as aerospace, automotive, and manufacturing for producing components with tight tolerances.
DECOILING
Decoiling is a crucial initial step in metal processing, involving the unwinding and straightening of coiled metal sheets or strips. This preparatory process ensures a consistent and manageable material feed for subsequent manufacturing operations. By unwinding coiled materials, decoiling contributes to precision in manufacturing, allowing for uniformity in the production of components. This efficiency enhances overall productivity by seamlessly integrating coiled materials into downstream manufacturing equipment.
Decoiling machines are versatile, capable of handling a wide range of materials and thicknesses, providing manufacturers with flexibility across various industries and applications. Ultimately, decoiling plays a pivotal role in streamlining metal fabrication processes and ensuring optimal performance in subsequent manufacturing stages.
SLITTING
Slitting is a metal processing technique that involves the precise cutting of wide coils or rolls into narrower strips. This process is crucial for industries requiring materials in specific widths, such as those used in the production of various metal products.
Slitting machines are equipped with multiple circular blades that make parallel cuts along the length of the coil, producing strips with accurate widths. The versatility of slitting extends to different materials, including metals, plastics, and textiles. This technique enhances material utilisation, reduces waste, and facilitates efficient downstream manufacturing processes.
Slitting is a key operation in industries like metal fabrication, packaging, and construction, where precise strip dimensions are essential for the production of diverse components and products.
SURFACE FINISHES
Polyester powder coating is a durable finishing method for metal surfaces, involving the electrostatic application of dry powder composed primarily of polyester resin. Once applied, the substrate undergoes curing in an oven, melting the powder into a smooth, protective film. This coating provides excellent resistance against corrosion, UV radiation, and chemicals, making it suitable for both indoor and outdoor applications.
With a wide range of color and finish options available, including matte, gloss, and textured varieties, polyester powder coatings offer versatile customisation to meet specific aesthetic and performance needs. Moreover, they are environmentally friendly, emitting minimal volatile organic compounds (VOCs) and hazardous air pollutants during application and curing, aligning with sustainable manufacturing practices and regulatory standards.
vertical saw
A vertical saw is a specialised cutting tool designed for precise vertical-axis cutting, preserving intricate patterns and three-dimensional structures in materials. With a vertically moving blade, it ensures accurate and controlled cuts without flattening edges, making it particularly valuable in industries like architecture. The tool’s versatility extends to various materials, including metals, plastics, and composites.
Equipped with features like variable speed controls, advanced cutting techniques, and safety measures, the vertical saw offers customisation and efficiency in applications requiring the maintenance of high-profile architectural designs. Its vertical orientation enhances accuracy, making it an essential tool for projects demanding precision in cutting complex patterns.
POWER PRESS
A power press, or mechanical press, is a vital manufacturing tool known for its high precision and versatility. Operating on the principle of converting rotational motion into linear force, it excels in shaping and cutting materials with consistent accuracy. The machine’s adaptability extends across various materials, including metals and plastics, making it indispensable in diverse industries such as automotive and aerospace.
Noteworthy features include customisable stroke lengths and speeds, contributing to efficient and cost-effective manufacturing processes. With robust construction for durability and safety measures, such as emergency stops and guards, power presses ensure operator well-being and compliance with industry standards. Their automation compatibility enhances productivity, positioning power presses as key assets in modern manufacturing environments.
CTLL/BLANKING
Cut to length line (CTLL) or blanking is a high-efficiency manufacturing process used for mass production of precision sheet metal components. In this process, a continuous coil of sheet metal is fed through a series of connected dies or tools, where each station performs a specific cutting or forming operation. CTLL allows for the continuous and automated production of blanks or stamped parts with minimal material waste. This method is widely employed in industries like automotive and appliance manufacturing, where large volumes of identical parts are required.
CTLL not only ensures high production rates but also offers precision and consistency in producing intricate shapes and contours from a continuous sheet of metal. This process is a cornerstone in the efficient fabrication of various components for diverse industrial applications.
SHEARING
Shearing is a metal fabrication process involving the precise cutting of sheet metal along a straight line. This technique utilises a shearing machine equipped with blades, where one blade moves across the other to produce a clean, straight cut.
Shearing is widely employed in various industries due to its efficiency in creating uniform, straight-edge cuts on materials such as metals, plastics, and composites. The process is particularly suitable for producing components with defined lengths and widths.
Shearing machines offer versatility in handling different material thicknesses and can accommodate varying sheet sizes. Known for its speed and accuracy, shearing plays a vital role in metalworking, construction, and manufacturing, providing a reliable method for creating precise cuts in sheet materials.
SEAM/SPOT WELDING
Seam welding and spot welding are essential processes in metal joining and fabrication. Seam welding involves continuously welding along a linear joint, creating a durable and watertight seam. This method is particularly useful for fabricating cylindrical or longitudinal joints in materials like sheet metal.
Spot welding, on the other hand, involves the localised application of heat and pressure to fuse two or more metal sheets at specific points, forming discrete weld spots.
Both processes are widely employed in automotive, aerospace, and manufacturing industries for their efficiency, speed, and cost-effectiveness.
Seam welding ensures the creation of robust, leak-resistant seams, while spot welding excels in quickly joining sheet metal components, making them integral in mass production scenarios. The versatility of these welding techniques in handling various materials, including steel and aluminium, highlights their significance in achieving strong and reliable bonds for diverse industrial applications.
ROLLING
Rolling flat sheets into convex, concave, and cylindrical shapes involves feeding the material through a rolling machine with adjustable rollers. As the flat sheet passes through, the machine applies pressure, gradually shaping it into the desired form. This versatile process is crucial in manufacturing components like tubes, where specific shapes are essential. After rolling, quality control ensures precise dimensions, and additional processes such as welding or surface finishing may be employed for the final product. The efficiency and adaptability of rolling make it a fundamental method for creating diverse shapes in various industries.
COBOT
Our cobot revolutionises fabrication with its versatile capabilities and services, excelling in automating repetitive tasks like material handling, part positioning, and operating welding equipment. Its precision and consistency enhance productivity while reducing errors and downtime.
Our cobot also ensures safety by working alongside human operators in a collaborative manner. Its adaptability allows for easy integration into existing workflows, making it a valuable asset for improving efficiency and scalability in fabrication operations. Our cobot offers a flexible and cost-effective solution to meet the evolving demands of fabrication requirements.
GENERAL ASSEMBLEY/PACKAGING
General assembly encompasses the process of assembling individual components or parts to create a final product. This involves tasks such as fitting parts together, fastening them, and ensuring they meet quality standards. On the other hand, packaging involves preparing products for distribution or storage. This includes activities such as placing items into containers, adding protective materials, labelling, and sealing. Both general assembly and packaging are crucial stages in the manufacturing and distribution processes, ensuring products are assembled correctly, packaged securely, and ready for delivery to customers.
Our commitment to excellence in metalwork fabrication is unmatched, bolstered by our extensive capabilities and unwavering dedication to customer satisfaction. With a comprehensive suite of fabrication services, ranging from precision cutting to intricate welding, we stand ready to transform your metalwork visions into reality.

Get in touch today to discuss your project
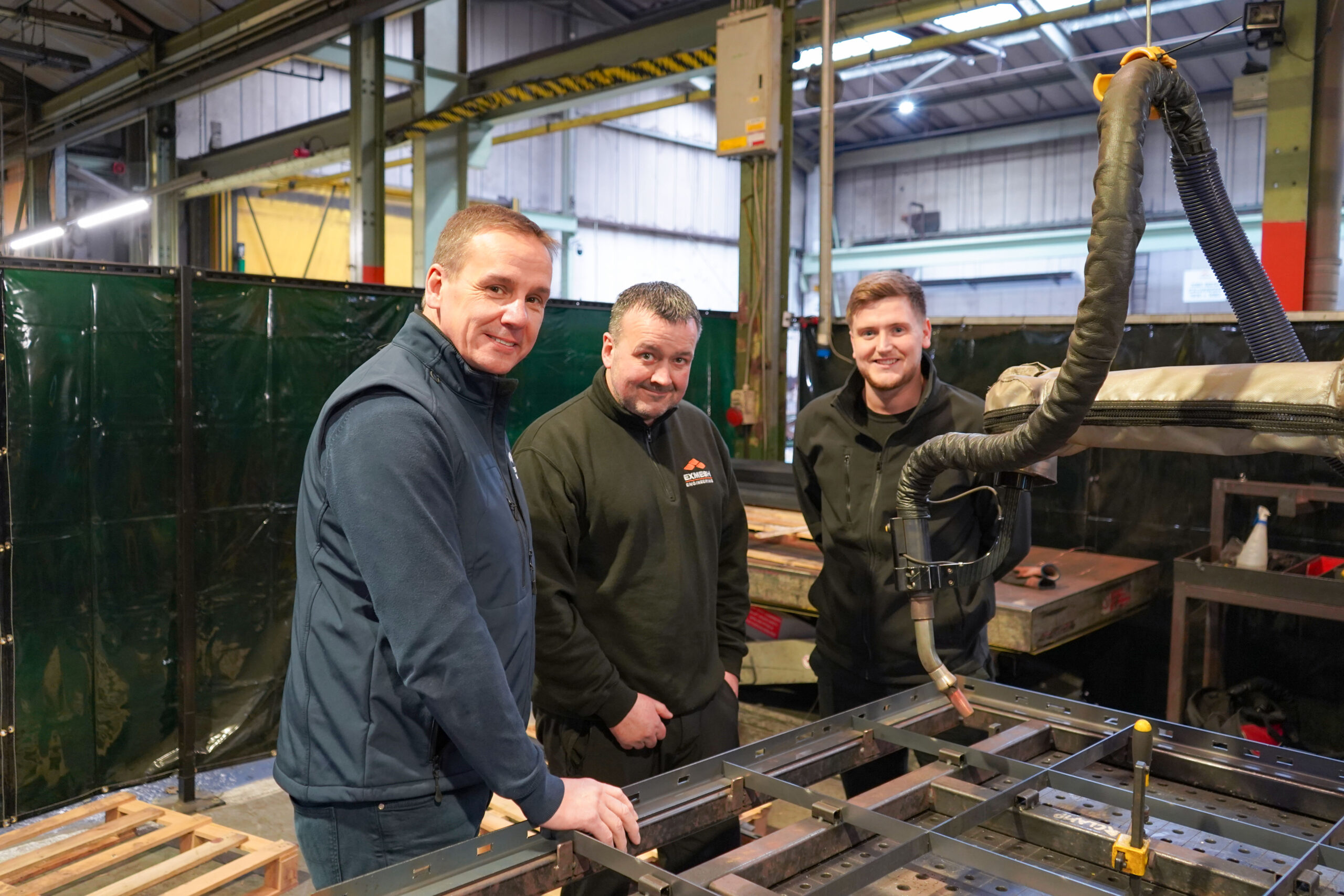